Die Live-online-Treffen im Arbeitskreis Wertanalyse / Value Management beim VDI Niederrheinsicher Bezirksverein zum Thema „Softwarebasiertes Cost-Engineering-Tool zur Unterstützung der Funktionsanalyse“ fanden mit den Fachbeiträgen der coscomp GmbH aus der Schweiz und fachlich fundierten Teilnehmerdialogen und Austausch von Praxiserfahrungen ein überdurchschnittlich großes Interesse.
Im Arbeitskreis Wertanalyse / Value Management (AK WA/VM) beim VDI Niederrheinischer Bezirksverein stand am 01. Dezember 2020 im Live-online-AK-Treffen das Thema Value-and-Cost-Engineering (VCE) zur Funktionsanalyse mit Beiträgen von der GmbH aus der Schweiz auf der Tagesordnung. Das Thema war für alle beteiligten im AK-Treffen so interessant, dass wir am 09. Februar 2021 mit den Referenten ein Folgetreffen verabredet haben. In dem 2. AK-Treffen wurde anhand einiger Praxisbeispiel das Thema VCE in der Funktionsanalyse und Wertgestaltungs- sowie Wertverbesserungsprozesse vertieft.
Value-and-Cost-Engineering (VCE)
Durch eine transparente Funktions- und Produktstruktur den Wettbewerbsvorteil sichern
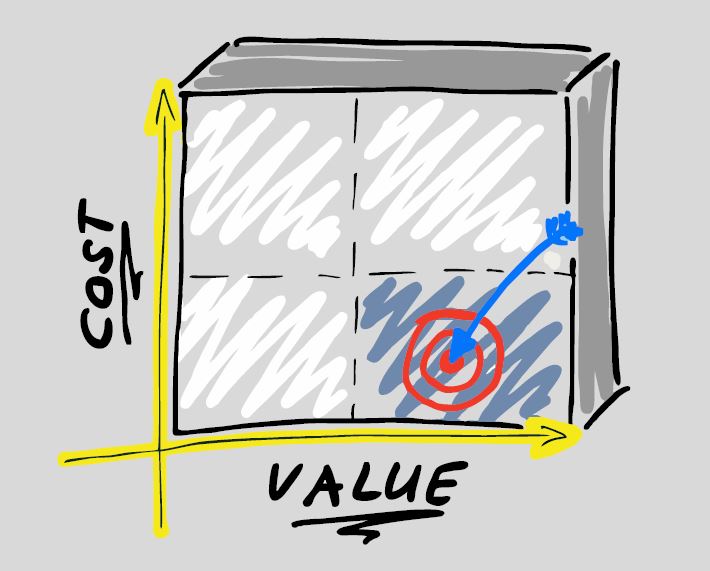
1. Entwicklungserfolg durch funktionsübergreifende Zusammenarbeit
Die globalen Märkte sind durch die aufkommenden Megatrends einem starken Wandel ausgesetzt. Dieser Wandel beeinflusst auf einer Seite die Geschäftsmodelle von Industrieunternehmen und hat auf der anderen Seite Auswirkungen auf das unternehmerische Handeln dieser Organisationen. Beeinflusst durch diesen Wandel können, traditionelle Strukturen in Produktmanagement, Entwicklung, Beschaffung, Fertigung und Montage nur schwer den heutigen Anforderungen an Transparenz, Agilität und Flexibilität gerecht werden.
1.1 Fehlende funktionsübergreifende Zusammenarbeit reduziert die Wettbewerbsfähigkeit in der Industrie
Durch die mehrheitlich konservativen Strukturen in Unternehmen werden Produkte erfahrungsgemäß ohne die Involvierung von Stakeholdern aus den nachgelagerten Unternehmensprozessen entwickelt. Durch immer kürzer werdende Produktlebenszyklen und die fehlende funktionsübergreifende Zusammenarbeit, können Herstell- und Komplexitätskosten im globalen Kontext nicht mehr wettbewerbsfähig gehalten werden und Industrieunternehmen aus verschiedenen Branchen geraten so unter Druck. Dieses Silodenken limitiert den Entwicklungserfolg jedes Produkts, da die Umsetzung so größtenteils auf die Erfahrungen und Möglichkeiten eines einzigen Entwicklungsingenieurs reduziert wird. Als Resultat entstehen Wissensbarrieren und die Herkunft eines bestimmten Produktes ist oftmals in den Endprodukten zu erkennen. Um ein Produkt von alteingefahrenen Vorbildern unabhängige Lösung zu finden, ist eine systematische Arbeitsweise erforderlich. Dies bedeutet, dass die Fähigkeit, Produkte markt- und kunden-zentriert zu entwickeln oder zu verbessern, eine entscheidende Differenzierungsquelle und somit ein Wettbewerbs-vorteil für jedes Unternehmen darstellt. Dies wird insbesondere in einer Zeit von sinkenden Margen zunehmend wichtig.
1.2 Kunde und Wettbewerb müssen ins Zentrum der Entwicklungsarbeit gestellt werden
Dies bedingt aber, dass sich nicht nur die Unternehmen verändern müssen, sondern auch die Produkte und deren Produktentwicklungsprozess. Der Grund dafür ist einfach. Früher reichte es aus, ein gutes Produkt auf dem Markt zu lancieren, welches sich dann nahezu von allein verkaufte. Heute müssen dem Produktentwicklungsprozess und der Produktstrategie besondere Aufmerksamkeit geschenkt werden. Über den Erfolg eines Produkts entscheiden in der Regel die Zeit bis zur Marktreife und die spezifische Ausrichtung auf den Kunden sowie der Wettbewerb.
2. Abstimmungen mit dem Kunden, Wettbewerb und Unternehmen ist, eine Herausforderung für die Produktentwicklung
Die Produktentwicklung zeigt sich in unterschiedlichen Umsetzungsformen und die Realisierung erfolgt firmen- oder branchenspezifisch von der reinen Bauchentscheidung durch Experten bis zum komplexen Stage-Gate-Delivery-Prozess in der Automobilindustrie. Desgleichen erfolgt die Messung eines entwickelten Produkts, oftmals erst mit der Auswertung der Deckungsbeiträge und Umsatzzahlen. Dies können sich viele Unternehmen in Zukunft nicht mehr leisten. Dement-sprechend stellt sich die Frage, wie Fehlschläge und daraus resultierende Produkte mit zu geringen Margen vermieden werden können.
2.1 Value-and-Cost-Engineering bringt die Produktkosten und Kundennutzen in Einklang
Mit dem systematischen und nachhaltigen Ansatz des Value-and-Cost-Engineerings wird das Verhältnis vom Beitrag einer Funktion zur Befriedigung der Nutzerbedürfnisse mit den anfallenden Herstellungskosten eines Produktes in Einklang gebracht. Somit steht der Zusammenhang zwischen dem Wert (Nutzen) eines Produktes für den Kunden gegenüber den eingesetzten Ressourcen im Fokus und eine einseitige Betrachtung der Kosten kann ausgeschlossen werden. Mithilfe der methodischen Gestaltung einer Systemarchitektur (siehe Fig. 1) können bereits in einer frühen Entwicklungsphase mögliche Relationen zwischen Anforderung, Funktionen und Produktstruktur hergestellt wer-den. Dabei spielt die funktionsübergreifende Zusammenarbeit eine wichtige Rolle für den späteren Produkterfolg und somit für die Wettbewerbsfähigkeit eines Unternehmens. Häufig werden aber Akteure der nachgelagerten Unternehmensprozesse nicht in die frühe Entwicklungsphase eines Produkts miteingebunden. Dies wiederum limitiert das einheitliche Systemverständnis der beteiligen Fachleute für die Entwicklungsaufgabe. Dadurch werden die Kos-ten für neue Werkzeuge, Montageprozesse oder die Anzahl und Varianz an Zulieferern schon in einer frühen Phase festgelegt und können später nicht ohne erheblichen Zusatzaufwand optimiert werden.
Deshalb sollte bereits in einer frühen Entwicklungsphase ein interdisziplinäres Kernteam zusammengestellt werden, welches das Ziel verfolgt, die Herstellkosten eines Produkts wettbewerbsfähig zu halten. Erfahrungsgemäß hat ein einheitliches Systemverständnis der beteiligten Fachleute das Potenzial, die vielfältigen Aspekte zu integrieren und die Akteure in der komplexen Produktentwicklung zu orchestrieren.
2.2 Praxiserprobte coscomp-Methode führt zu transparenten Funktionskosten
Durch softwarebasierte Cost-Engineering-Tools, welche den Ansatz einer parametrischen Kostenanalyse verfolgen, werden aus der Funktions- und Produktstruktur, transparent die Funktionskosten abgeleitet. Der Kundennutzen (das Nutzerbedürfnis), dementsprechend der Wert eines Produkts, beeinflusst durch die Verbesserung von Funktionen direkt die Herstellkosten eines Produkts. Im Kontext von Neuentwicklungen und Redesign-Aktivitäten werden ergänzend Kreativitätsmethoden wie Design-Thinking oder die Ideation-Toolbox von Wallas angewendet, um das Potenzial in einem kollaborativen Ansatz zusammen mit den beteiligten Fachleuten auszuschöpfen.
2.3 Klare Systemarchitektur ermöglicht transparente Darstellung der Funktionen und ihrer Zusammenhänge
Mithilfe einer vereinfachten systematischen und praxiserprobten Vorgehensweise wird aufgezeigt, wie die Value-and-Cost-Engineering Methode von coscomp funktioniert. Durch den Aufbau einer Systemarchitektur (siehe Fig. 1) werden das Wettbewerbsumfeld und die Anforderungen des Marktes analysiert, und in technische Funktionen über-setzt. Darauf aufbauend werden softwarebasierte Cost-Engineering-Tools eingesetzt, um valide Funktionskosten ab-zuleiten (siehe Fig. 1). Durch den Einsatz softwarebasierten Cost-Engineering-Tools, können Entscheidungen systematisiert werden, welche sonst ausschließlich auf dem ‹Bauchgefühl› von Experten beruhen. Die Funktionen und die technischen Baugruppen werden mit Preisschildern versehen. Ausführliche Kundenbefragungen und Workshops mit definierten Stakeholdern, welche auskaufenden, verlorenen sowie Kunden von Wettbewerbern bestehen, ge-ben Aufschluss über die geforderten Funktionen und die damit verbundene Zielkostenstruktur eines Produkts.
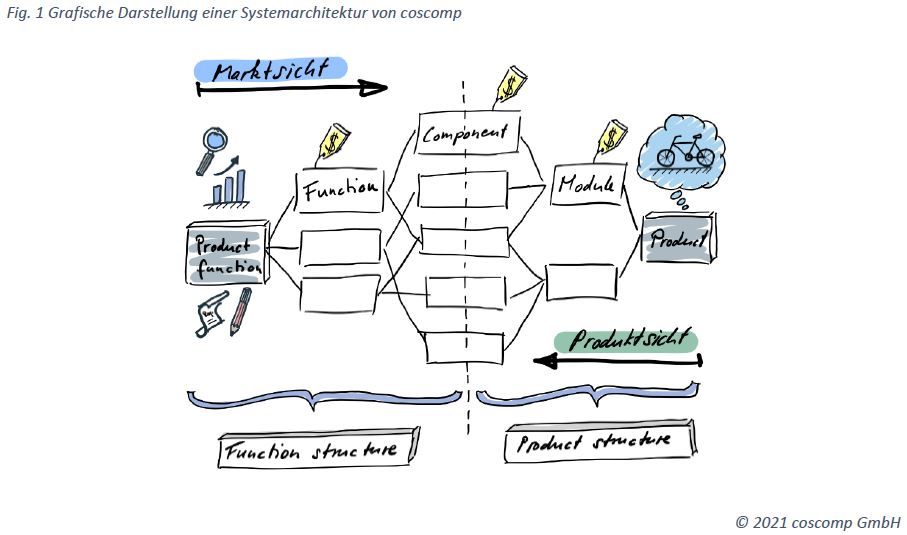
2.4 Kosteneinsparungen bis 30 % und tiefere Lead Time durch den Einsatz der coscomp-Methode
Wird die coscomp-Methode bei der Neuentwicklung eines Produkts eingesetzt, können Kosteneinsparungen von bis zu vierzig Prozent EBIT-wirksam erzielt und die Time-to-Market um bis zu fünfzig Prozent reduziert werden. Der Grund liegt unter anderem darin, dass seit mehreren Dekaden bekannt ist, dass die Produktentwicklung rund siebzig bis achtzig Prozent der Aufwände und möglichen Handlungsspielräume der nachgelagerten Unternehmensprozesse wie Beschaffung, Fertigung, Montage, Wartung und Instandhaltung festlegt. Diese Erkenntnis in Kombination mit der Schaffung eines frühen einheitlichen Systemverständnisses der Entwicklungsaufgabe mit allen beteiligen Fach-kräften, ist eine wichtige Voraussetzung, um die Potenziale zu heben. Bei einem Redesign von Produkten liegt die mögliche Kosteneinsparung durch bereits bestehende Produktstrukturen bei ca. fünfzehn Prozent. Die folgende Darstellung (siehe Fig. 2) visualisiert, welches die Kosten- und Komplexitätstreiber einer gewünschten Funktion (Anforderung) sind. Die Herstellkosten können nur zielführend gemanagt werden, wenn diese Zusammenhänge und deren Komplexität detailliert verstanden werden.
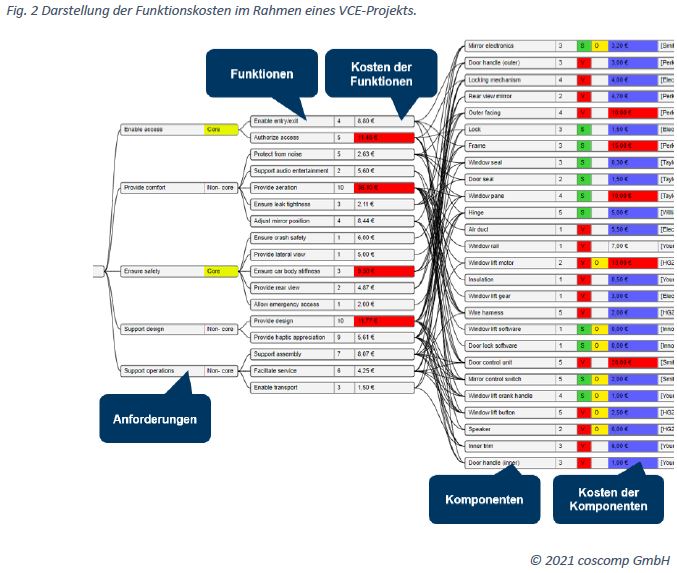
3. Praxiserprobter Ansatz brachte eine Herstellkostenreduktion von über 30 %
Im nachfolgenden Practical Case wurde ein Produkt aus dem Portfolio eines international agierenden Unternehmens in der Maschinenindustrie gezielt überarbeitet und neu auf den Markt ausgerichtet. Dabei konnten die Herstellkosten um über dreißig Prozent gesenkt werden.
3.1 Ausgangslage
Ein Schweizer Maschinenbauunternehmen, das weltweit Maschinen und Anlagen fertigt und vertreibt, geriet im zunehmend globalisierten Wettbewerb durch asiatische Mitbewerber unter starken Kostendruck. Das spezifische Produkt wies aufgrund der sinkenden Verkaufszahlen und Preise eine immer geringere Marge auf. Weder der inter-national bekannte und angesehene Brand noch die kommunizierten Alleinstellungsmerkmale (Unique-Selling-Proposition) des spezifischen Produkts konnten die Negativbewegung stoppen.
3.2 Redesign-Ansatz von coscomp
Mit dem Aufbau einer Systemarchitektur und der Analyse von Funktions- und Produktstruktur, wurde gemeinsam mit dem Kunden eine Kostenreduktion und Neuausrichtung des fraglichen Produkts durchgeführt und begleitend eine VCE-Organisation aufgebaut. Ebenso wurde ein funktionsübergreifendes Projektteam aus Arbeitskräften der nachgelagerten Unternehmensprozessen zielgerichtet zusammengestellt und Verantwortlichkeiten definiert.
Aufbauend auf dem Projekt-Set-up sammelte das beteiligte Team im Ansatz des Desk-Research alle notwendigen Daten bezüglich der Margen- und Kostenentwicklung in den Märkten sowie der Wettbewerber, Kunden und Trends. Fehlende Informationen wurden durch Primärforschungsergebnisse (Stakeholderinterviews) erhoben. Das Bench-marking sowohl mit eigenen Produkten als auch mit Produkten des Wettbewerbs sowie die Ergebnisse aus der Stakeholderbefragung erlaubten es, Defizite zu identifizieren und erste Maßnahmen abzuleiten. Durch den Aufbau der Systemarchitektur wurden die Anforderungen des Marktes analysiert und in technische Funktionen übersetzt. Mit-hilfe eines parametrischen Cost-Engineering-Tools, wurden die Herstellkosten der Komponenten ermittelt und dar-aus die Funktionskosten über eine mathematische Formel abgeleitet. Durch die Design-Thinking-Methode ließen sich Maßnahmen identifizieren, die die geforderten Funktionen erfüllten und gleichzeitig deren Kosten reduzierten. Dies erfolgte in zweiwöchentlichen Deepdive-Workshop-Sessions mit strikten Timekeeper-Gates und dem Erstellen von Rapid Prototypes, angelehnt an den Stanford Design Innovation Process (siehe Fig. 3). Ein begleitendes Maßnahmentracking für das gesamte Projektteam sowie ein Cockpit von Key-Performance-Indikatoren (KPI) für das Management, sicherten eine Fertigstellung des Redesigns im vorgegebenen Zeit-, Qualitäts- und Kostenrahmen.
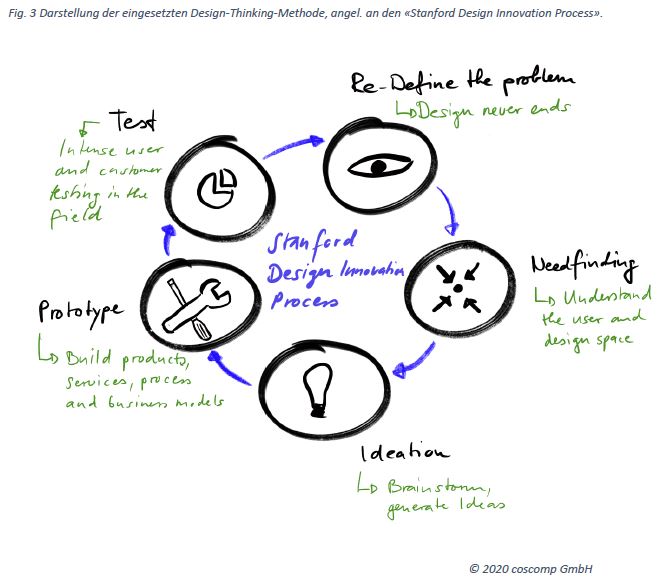
3.3 Ergebnis
Im Rahmen des zwölfmonatigen Projekts konnten die Herstellkosten (Material- und Fertigungskosten) des spezifischen Produkts um dreißig Prozent reduziert werden. Wesentliche Hebel lagen dabei in der Überarbeitung von Baugruppen in Zusammenarbeit mit verschiedenen Lieferanten und dem Fokus auf Fertigungsfreundlichkeit. Ein beim Kunden parallel aufgebautes Value-and-Cost-Engineering-Team wurde in den erforderlichen Methoden und Tools geschult, um so langfristig interne Fähigkeiten und Kompetenzen aufbauen zu können.
Kontakt:
coscomp GmbH
Chaltenbodenstrasse 6C
CH-8834 Schindellegi
www.coscomp.ch
Über den Autor:
Der Autor begann nach der Lehre als Polymechaniker, ein Maschinenbaustudium an der Höheren Fach-schule und arbeitete berufsbegleitend als Entwicklungsingenieur bei verschiedenen Unternehmen im Maschinen- und Anlagenbau. Seine Diplomarbeit absolvierte er in der Automobilindustrie. Nach dem Ab-schluss bekleidete der Autor verschiedene Funktionen im Projekt- und Produktmanagement. Parallel zu seiner Arbeitstätigkeit absolvierte er den MBA in Entrepreneurial Management an der Universität in Liechtenstein und analysierte in seiner Masterthesis einen möglichen Markteintritt für den indischen Automobielmarkt. Das MBA-Studium weckte bei ihm das Interesse am Thema Innovation und Entrepreneurship. Dadurch begann er im Jahre 2016 das gleichnamige PhD-Studium an der ISM in Paris und widmete sich in den letzten Jahren der Transformation des Produktentwicklungsprozesses durch zukünftige ‹smart, connected Products› mit dem Fokus auf Innovationsmanagement, Systems-Engineering und dem Value-and-Cost-Engineering.
Raphael Schlup
Value-and-Cost-Engineer / Systems Engineer / Data Analyst / CTO
T: +41 58 501 62 64
M: +41 79 360 28 64
raphael.schlup@coscomp.ch